Photothermal Radiometry
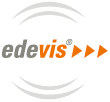
![]() |
Photothermal Radiometry
Photothermal radiometry is a non-contact and nondestructive testing method for hardness measurements (e.g. hardness profiles of case-hardened steels). Other applications are measurement of coating thickness, coating adhesion or detection of grinding burns. Whenever surface layers are altered by mechanical, chemical or heat treatment, photothermal radiometry can be considered for characterization. This technique is much faster than metallographic analyses, thus enabling inline hardness inspection. Even complete hardness depth profiles can be reconstructed for laboratory purposes.
Typical Applications:
Hardness testing:- Measurement of case hardness depth (CHD)
- Hardness depth profiling of coatings
- Measurement of coating thicknesses
- Detection of delaminated coatings
- Detection of hidden corrosion
- Other Applications
- Detection of the grinding burns
- Porosity Quantification
- Testing of the welding joints
![]() |
The principle of the photothermal radiography
The photothermal measurement method is based on the heating of the surfaces by laser light, intensity modulated or pulsed. During the excitation, the surface temperature is monitored by an infrared detector. The heat generated diffuses in the sample. The detector measures the resulting surface temperature, which depends on the material parameters and the sample geometry. An amplifier with synchronization (lockin) extracts the phase information of the infrared signal. Using calibration measurements, the phase can be correlated with certain material parameters, such as hardness or thickness of the coating. Therefore, the system must be calibrated with destructive measurements on the sample material and geometry.
The measurement time depends on the type of application
- Classification of the depths of the cemented layer at a certain modulation frequency between 10 and 30 seconds. Reconstruction of a hardness profile at a depth between 15 and 40 minutes
![]() |