Testing of adhesive joints for composite materials
Specifications
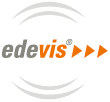
Testing of Adhesive Joints
![]() Defective bonding of a fin in a light aircraft wing |
Bonding processes allow the joining of different materials and at the same time avoid damage of the join partners. These and other advantages have led to a wide distribution in the fields of aerospace, automotive, boat building and wind turbines. Shearography is one of the few methods that is suitable for testing of adhesive joints, as it is sensitive to the local mechanical properties of the join connection.
|
|
|
![]() |
Principle
For shearographic testing, the object surface is illuminated with laser light. By interference, a characteristic pattern (‘speckle pattern’) is generated. The shearography camera captures changes of this pattern which occur when the object deforms under a small load. Due to the special beam path the measurement result is not the absolute displacement, but its derivative in a defined direction which is determined by the shear vector. Thus, shearography is significantly more robust than other interferometric testing methods. By adjusting the amount and direction of the shear vector, the sensitivity and the sensitivity direction of the method can be adjusted. Although only the surface is measured, deeplying bonding defects can also be detected as long as they affect the deformation behavior of the component.
![]() |
The System
The measurement of the object deformation is done in a non-contact way. The system complies with laser class 1 and is therefore safe to handle for trained users. Depending on the application, the loading of the component is generated by heat, vibration or pressure change. The excitation is always nondestructive, typical loads are 5 ° C temperature difference or 50 mbar pressure difference, respectively. The system is very flexible and mobile, the expenditure on equipment ranges from a mobile solution with a laptop to a fully integrated vacuum hood. Defects can be detected reliably and quickly, a test usually takes only a few seconds. The measurement field size is determined by the available laser power, the required resolution and the type of excitation and can be up to 1 m2 .
![]() Bonded steel sheets: Good bonding (left), missing adhesive (right) |
Applications
The application fields are very diverse, ranging from aerospace to automotive, to boat building and to wind turbines. Defects like interruptions/narrowing of adhesive bead, air inclusions, excess resin (e.g. in honeycombs) and kissing bonds can be detected if they affect the local mechanical behavior of the component. The test can be performed large-scale and in a non-contact way (depending on the excitation method). Shearography is particularly well suited for the testing of bonded plastics, fiber-plastic composites, honeycomb and foam sandwich parts, but it can also be used to test adhesive joints of metal.
![]() GFRP/foam horizontal tail of light aircraft with defetive bonding: Narrowing and interruption of spar bonding (a: shearogram, b: shearogram after unwrapping and highpassfiltering) |