Testing of CFRP components
Specifications
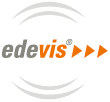
Testing of CFRP components
![]() |
Testing of aerospace structures
Many modern aerospace structures are made of fiber composite materials. During production and maintenance many different non-destructive testing methods are used to ensure the safety of the components. Active thermography is an efficient method for rapid inspection of large areas in a non-contact way. Due to the layered structure of composites, many different kinds of defects - which are entirely different than the ones in metals - can occur: delaminations / debondings between layers, air inclusions (porosity) and impacts, etc. Impacts are particularly critical because they are barely recognizable from the outside even though severe damage may be present inside. Optically excited thermography methods can reliably detect those defects and therefore play an increasingly important role in the investigation of safety-relevant components.
|
|
![]() |
Principle
Optically excited lock-in thermography uses halogen lamps to periodically heat up the surface of the tested structure. A thermal imaging camera captures the changes of surface temperature. The recorded temperature profiles at each pixel are Fourier transformed and a result image is calculated in real time. The time shift (phase) between heating and temperature depends on how fast the heat flows into the inside of the component. The resulting image (phase image), in which the phase delay is colorcoded, reveals hidden boundary layers and thermal structures. The depth range is determined by the modulation frequency of the heating and is therefore adjustable within wide limits. A practically relevant advantage of phase images is that the optical and/or infrared surface structures of the test object (emission coefficient, inhomogeneous temperature distribution) can be suppressed by the run-time evaluation. Thus, the phase image almost exclusively shows sub-surface structures.
![]() |
The large-area excitation of components is achieved with halogen lamps that require no special requirements on labor protection. The method works completely contact-free, so component damages cannot occur. Since the diffusion length is directly dependent on the modulation frequency, depth-resolved measurements are possible. The maximum depth range in CFRP is around 5 to 6 mm. The required test time depends on the component thickness and the thermal diffusivity of the inspected material. For testing of CFRP, typical measurement times are between 30 seconds and a few minutes per square meter.
![]() |
ApplicationsAll safety-relevant aircraft structures must be tested non-destructively, both during production and operation. There are many different types of material flaws that strongly depend on the material used. Typical applications in the field of fiber reinforced plastics / ceramics are inspections for delamination, impacts, inclusion of other materials (er.g. entrapped water in honeycomb structures), determination of porosity, resin / fiber contents, wall thickness, fiber orientation and inhomogeneities. Another important application is the testing of adhesive joints, particularly the characterization of the bonding of metallic insert to the overlying laminate.
![]() Porosity in a CFRP fuselage shell - detected with optically excited lockin thermography
|
![]() Water inclusion in a CFRP sandwich structure
|